- 藤田鐵工所沿革
- 製品と技術の変遷
- 社長メッセージ
藤田鐵工所は
創業110周年を迎えました
大正3年1914
個人経営を以て創業、製茶機械ならびに工作機械を製作販売
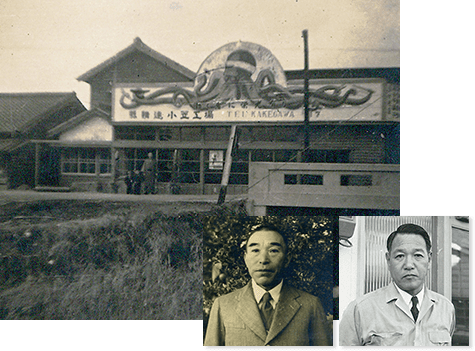
昭和16年1941
日本楽器製造(株)協力工場として軍事品(航空機部品)を製作
昭和20年1945
運輸省名古屋鉄道局管内の機関車部品を製作
昭和24年1949
各社の自動二輪車部品の製造を開始、特にクランクシャフト、コンロッド、及びシャフト類の鍛造より切削、熱処理、研削完成まで一貫加工の基盤を確立
昭和26年1951
株式会社藤田鐵工所に法人改組、自動二輪車部品の増産に対処すべく業容を拡大
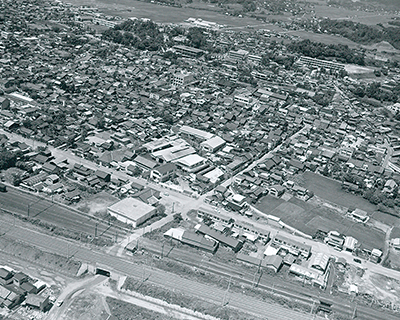
昭和35年1960
同系会社 大和鍛工(株)を設立
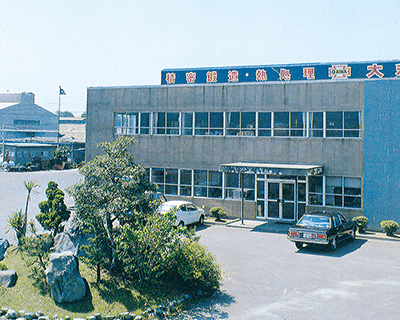
昭和39年1964
社内鍛造金型製作部門を分離して(株)富士金型製作所 を設立
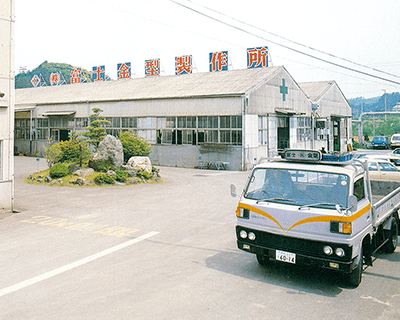
昭和45年1970
業容拡張のため工場を分離し、南工場と命名創業を開始
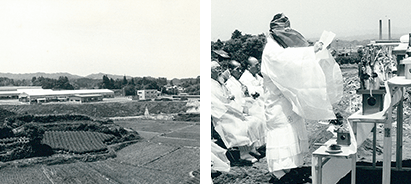
昭和46年1971
企業内技能養成機関として静岡県知事認可「藤田高等職業訓練校」(鍛造科2年制)を開設
昭和52年1977
心身障害者雇用促進月間に労働大臣表彰を受く
昭和53年1978
同系会社 聖和熱処理工研(株)を設立
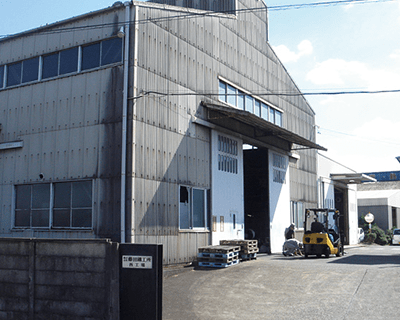
昭和56年1981
「第1回静岡県中小企業小集団活動事例発表大会」に参加
最高賞の静岡県知事賞を獲得
昭和61年1986
クランクシャフト、コンロッド加工専用機及びオートローダー用ロボットの本格的自社開発製造を開始
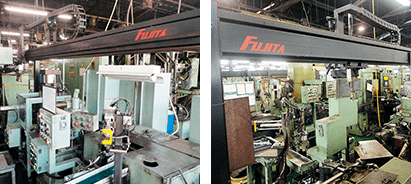
平成3年1991
同系会社 (株)フジタ を設立
3軸自動ホーニング機を7~8年かけて10台導入
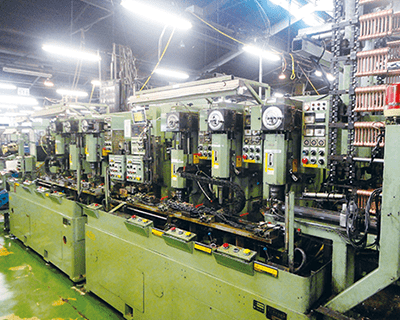
平成5年1993
社会保険事業の推進発展に寄与した功績に対し、功労事業所として社会保険庁長官表彰を受賞
平成7年1995
小型エンジン用のクランクサブASSY機(くみ子)を製作
平成9年1997
割型コンロッドの加工を開始
平成10年1998
インドへ技術指導の事業開始
南工場に加工工場(中工場)を増築
平成12年2000
優良申告法人表敬状を受賞
平成14年2002
インドネシアに PT.FUJITA INDONESIA を設立
聖和熱処理工研(株)を藤田鐵工所に併合して西工場とする
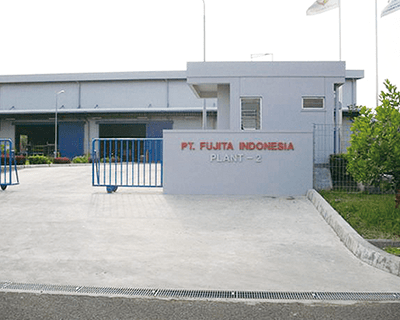
平成16年2004
(株)藤田鐵工所がISO14001を取得
平成17年2005
(株)藤田鐵工所がISO9001を取得
南工場に加工工場(第5工場)を新設
インドネシアからの研修生の受け入れがはじまる
社内のQC発表会が100回を達成
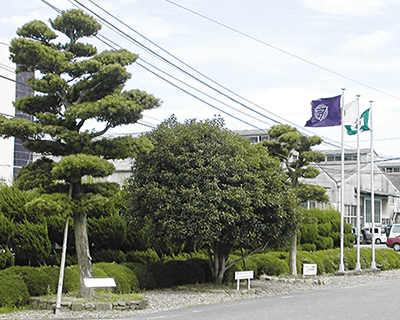
平成22年2010
ベトナムにFUJITA VIETNAM CO., LTDを設立
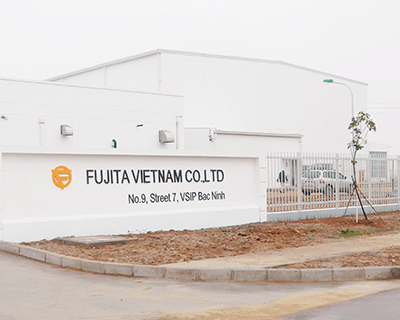
平成25年2013
南工場第一事務所の竣工
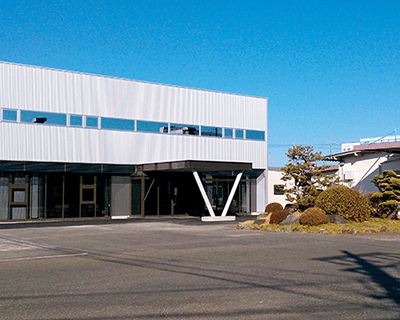
平成26年2014
創業100年となる
『静岡県障害者就労応援団』へ登録
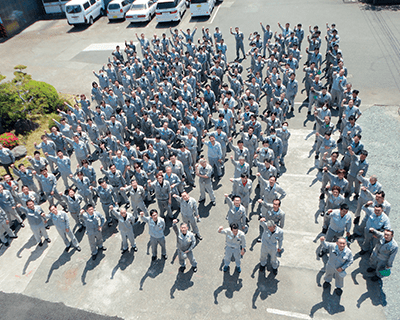
平成27年2015
掛川市と防災協定を締結
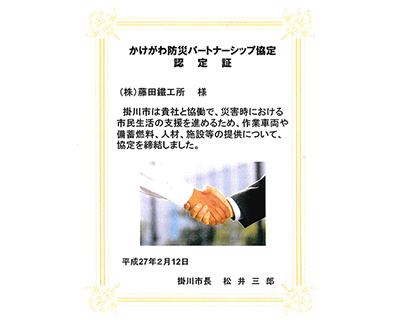
令和2年2020
掛川市『子育てに優しい事業所』に認定される
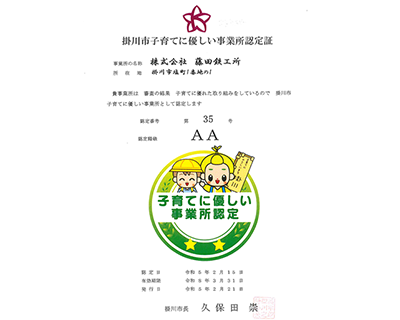
令和3年2021
『かけがわ健康づくり実践事業所』に認定される
令和4年2022
工機厚生棟を竣工
『ふじのくに健康づくり推進シルバー事業所』に認定される
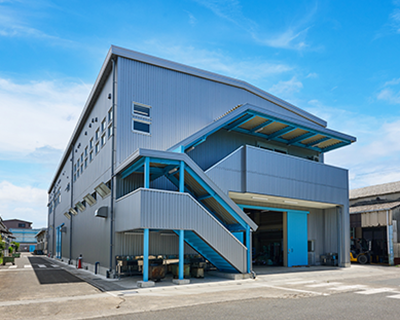
令和5年2023
本社機能を移転(掛川市塩町から掛川市久保)
令和6年2024
1月4日 創業110周年を迎える
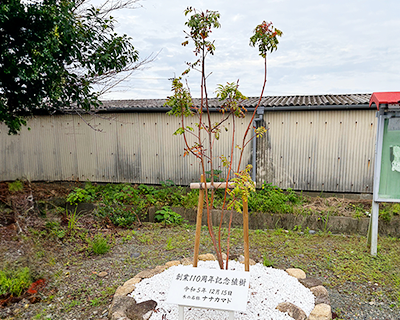
製品と技術の変遷
熱間鍛造から冷間鍛造へ
工場に新技術を導入
昭和40年代、工場に設置された鍛造ラインは熱間鍛造が主流であったが、刈払機やチェーンソーの小型クランクシャフトの素材整形は冷間鍛造へと様変わりしている。
これにより生産性向上や省エネルギー化を実現できた。
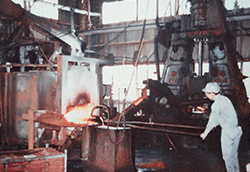
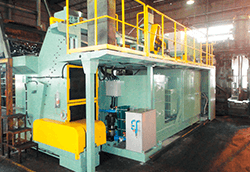
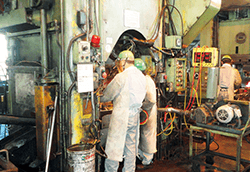
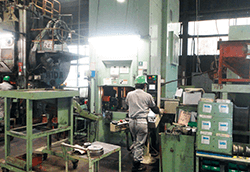
失敗の連続にも負けず挑戦した
小型クランク加工の自動化
当時はエアシリンダー、ハンド等の市販品が少なく、不良品発生につながるトラブルもあった。そのため専用機の内製化、工場の自動化が進められた。苦労も多かったが、難題にも果敢に挑戦するという気概が養われた。
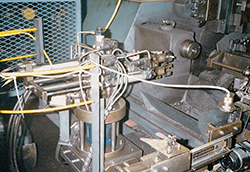
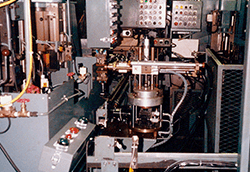
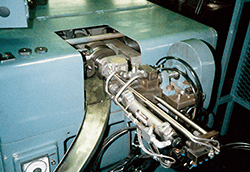
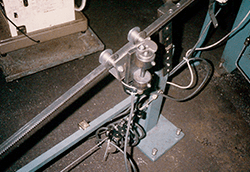
コンロッド並行
捩
れ矯正機開発
苦い経験も、次の目標へのワンステップ
コンロッドはエンジン部品のピストン軸とクランク軸を支える連接棒である。
熱処理によって強度を上げるが、その際コンロッドに歪みが生じるために、最終的にはその矯正が必要になる。
約5ヵ月かけて当社で設計した矯正機は、歪量を自動で測定して当時のFAコンピュータで演算補正させ、自動で矯正させるという優れものであった。
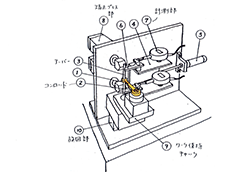
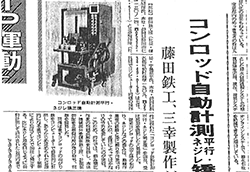
大量生産時代
海外向けチェーンソー用小型一体
クランク加工ラインの自動化
1987年、海外チェーンソーメーカーから受注した小型一体クランクは、受注数が多い割に機種が少なく、現在の多種少量生産では考えられない大量生産品だった。
納品に対応するために専用加工自動化ラインを社内工機課で製作、2ライン昼夜でフル生産した。
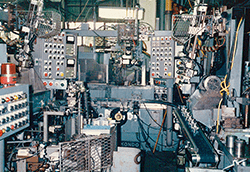
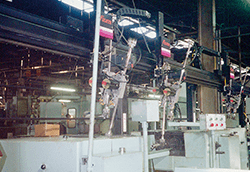
コンロッドトランスファーマシン開発
子どものおもちゃから
ヒントを得て独自開発
当時、自動生産方式のトランスファーマシンは専用の工機工場がなかったため、治工具製作部で一から製作した。
ワークを並べる方法は、上からボールを入れると筒の中をくるくる回りながら下へ落ちてくる幼児用のおもちゃからヒントを得ている。
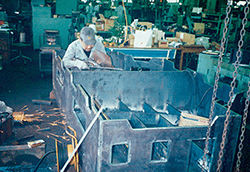
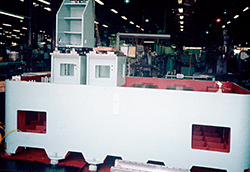
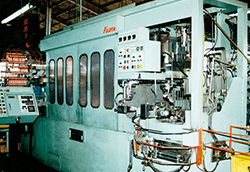
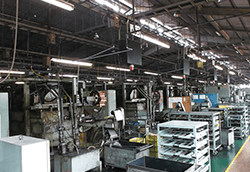
コンロッド加工に
3軸自動ホーニング機を導入、
従来機の2倍を生産
工機部門は製作時間を短縮するため、専用メーカーから3軸のホーニング機を10台導入して治具、自動搬送装置、自動測定装置等を社内で製作して組み立てた。
ワークの芯間距離(ピッチ)精度が出にくいといった苦労もあったが、それでも生産性は従来機の2倍を誇るようになった。
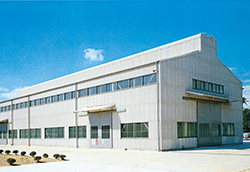
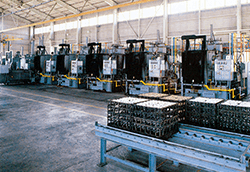
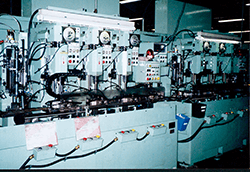
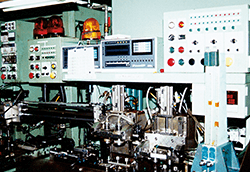
小型クランクシャフト
組立後研磨
逆転の発想で大幅生産性アップ
草刈機用小型クランクシャフトは研磨完成後、油圧プレスで組み立て、手作業で左右のクランクシャフトを矯正して同軸度の精度を出していたが、従来の工程を逆にして、組み立ててから研磨する自動化ラインを社内工機課にて製作して設置。手作業での芯だし作業をなくし大幅に生産性を上げた。
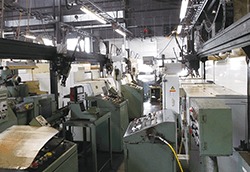
他間接ロボットを組み合わせたクランクシャフト自動組み立て機(くみ子)の製作
チェーンソーや刈払機の小型エンジン用のクランクサブASSY機1号、2号、3号機が社内で製作された。
この機械の完成によって組み付け能力が大幅にアップ。なお、組み立てる機械ということから、この機械を「くみ子」と命名した。
インド部品メーカへの技術支援
5名の社員で85日間
技術提携していたインドの部品メーカーに4台のコンロッド加工機を販売。また1998年の3月から6月までの85日間にわたり、5名の社員を派遣し現地指導に当たらせた。
インドの部品メーカーに対しては、その後も技術面などでいろいろと相談に乗ったり、アドバイスを行い、
刃具
の支給等も行った。
この経験が、のちの海外展開の役に立ち今日に至っている。
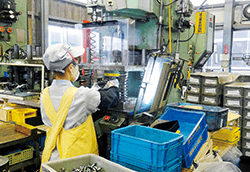
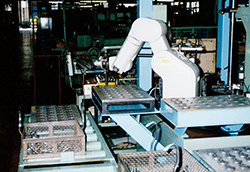
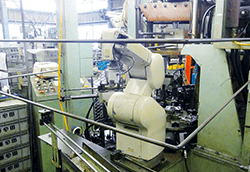
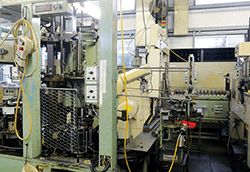
スポーツバイクの先陣YZF-R1の浸炭割型コンロッドに挑戦
1997年のミラノショーで発表された大型バイクYAMAHA YZF-R1(4XV)のハイスペックのエンジンには、軽量、高強度のコネクティングロッドが要求された。
ヤマハ発動機の設計との共同開発のかたちで、全浸炭の割型コンロッドの試作に挑戦。
HRC60を超える硬度の加工をどのようにしたらできるのか。生産技術陣は試行錯誤の末やっと試作品を収めることができた。
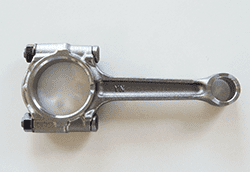
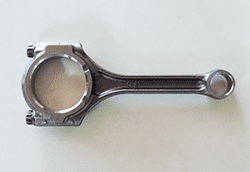
中工場に研磨自動化稼動
最新型NC研磨機を導入し、小型クランクを高精度自動加工
従来の油圧式倣い研磨機に代え、NC 装置で精密に砥石を成形、研磨する最新鋭研磨機を導入。
この研磨機に社内工機課で自動化装置(ローダー)と自動測定装置を取り付けて自動化、焼入材をファインボーリングするNC旋盤と組み合わせ小型クランク研磨自動化ラインを5ライン設置した。
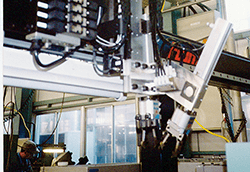
割型コンロッドの重量分類機・レーザーマーキング機で組み立て不良、未加工不良も検出
最初に開発した機械はワークストッカーの上に並べたワークをベルトコンベヤーが電子秤ばかりのところまで移動して重量を測定、さらに8分割のターレット式ハンコで捺印し、ロボットで分類整理する方式であった。
ただ、せっかく捺印した文字が消えてしまうという不具合が出ることもあったため、レーザーマーキングでの方式を採用することになった。
その後、CCD カメラによる画像処理装置を組み付け、組み立て不良、未加工不良を検出できるようにして、さらなる品質の向上に努めた。
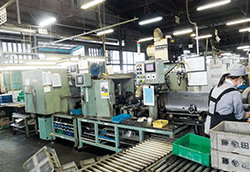
割型コンロッドの生産性を追求
多関節ロボットによる自動化ライン完成
割型コンロッドは加工工程数が多く、生産性のアップが求められたため2006年に専用加工機を整備した。
その後もコストダウンと生産性アップを推進するための自動化に取り組み、2010年には、多関節ロボットを駆使した自動化ラインへと変わっていった。
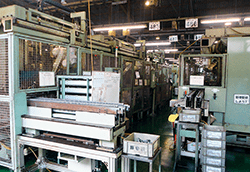
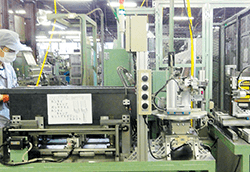
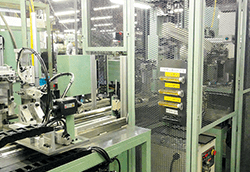
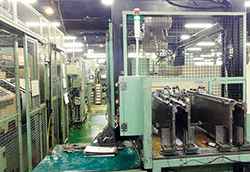
焼入材も“まっぷたつ”NC 制御の熱処理試験片カット機製作
従来、高周波焼き入れの組織検査で試験片をカットするには、市販の砥石式切断機(手動式)を使用し、クランクシャフトの切断に2~3時間付きっきりの作業が必要であった。途中で砥石が割れてしまうというトラブルも多発していた。
社内工機課で製作した切断機は、NC制御で作業者が付いていなくても試験片を切断する。好評につきベトナム工場用の2号機も製作した。
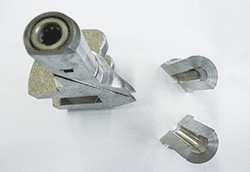
トルク特性をデータ化しグラフ解析を可能としたクランクシャフトのトルク試験機製作
従来、組み立てたクランクシャフトのトルク(耐性捩れ強度)は、長い棒にバネ秤を取り付け、人の手で測定していた。
この年、トルク試験機を社内工機課で製作し、トルクデータを数値化して寸法精度、組立条件との関係を解析できるようにした。
クランクシャフトの重要な性能であり、取得したISO9001トレーサビリティ項目の遵守にもなった。
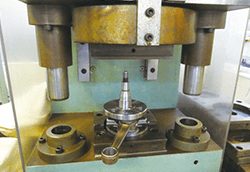
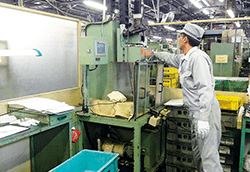
鍛造品の外観をカメラで検査
画像処理自動外観検査機フラッシュ・アイ製作
従来、鍛造品の外観欠陥検査は人手作業。目で見て検査していたが、フラッシュ・アイにより高速画像処理による検査を可能とした。その後、定数をパレットに並べていくことまでを自動でできるようにした。この頃より、高度なエレクトロニクス技術により、従来に無い新しいタイプの機械も製作が可能となった。
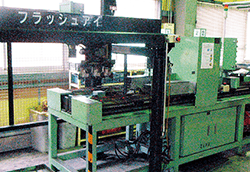
検査機の変遷
アナログ測定器からデジタル化
解析精度の向上が進行中
検査機はデジタル化とともにデータ処理時間も短縮され、機器もコンパクトになった。
近年では、メーカーが、測定機器を指定することもあり、さらに硬度、寸法測定の他、コンタミ測定も要求され、品質要求はますます高くなっている。グローバル競争を勝ち抜くためにも、100%良品である品質を保証できる体制を整えている。
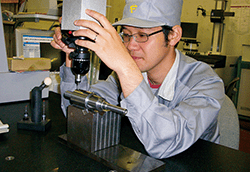
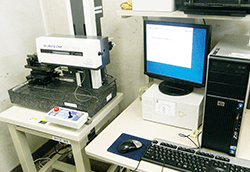
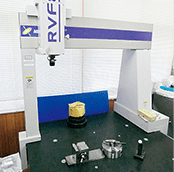
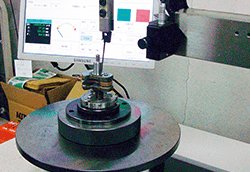
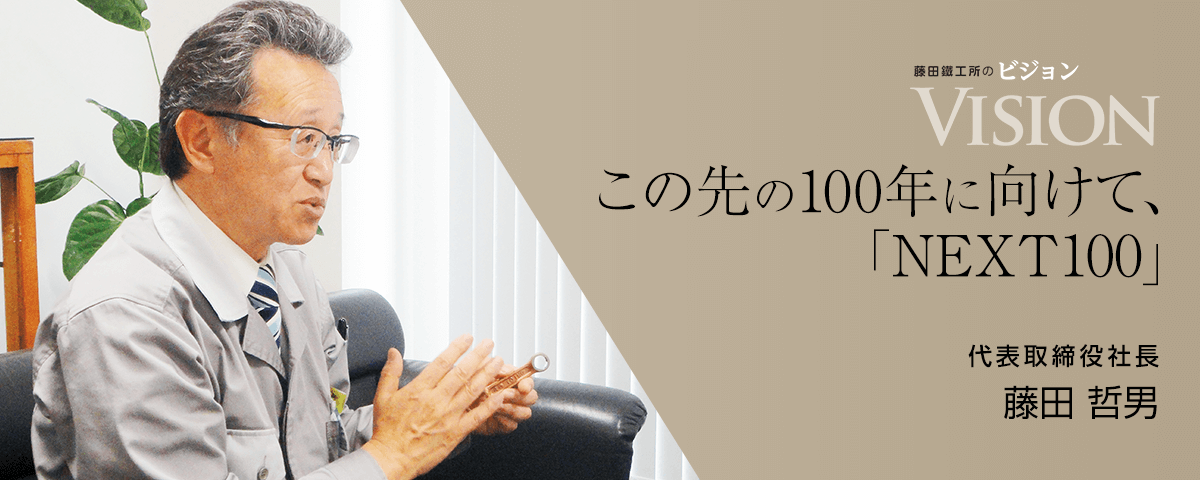
厳しさ増す経済環境
藤田鐵工所が 呱々 の声を上げて1世紀、日本も世界も大きな変貌を遂げてきた。当社がこの100年、創業当時と全く同じことをしていたならば、当然、今とは全く違う姿となっていた。時代や社会の変化に合わせてチャレンジし、チェンジしてきたことで、現在の姿となったのである。
日本は先進的技術の国として海外から高い評価を得て、成長、発展してきた。しかし、最近の製造業を取り巻く環境は人件費、エネルギーコスト、原材料費の高騰などによって厳しさを増している。加えて少子高齢社会などで国内需要の大きな伸びは考えにくくなっている。
当社も新たな市場の開拓、経営の効率化を求め、インドネシアやベトナムでの現地生産を行ってきた。経済のグローバル化が進展していくなかで、今後も生産拠点の海外移転の流れが加速すると予測される。かつては国内企業をライバルとしていたが、これからは海外企業も新しいライバルとして加わってくる。
グローバル化していくなかでもう一つ大切なことは、我々の日常生活とは縁がないように思われていた世界のどこかで起きる事件や紛争が、実は我々の生活に影響を与えるようになってきたことである。遠い世界での紛争によって、商品の輸出がストップすれば、その商品に使われている部品の供給もストップせざるを得なくなる。売り上げの減少は我々の暮らしに直接響いてくる。情報の迅速な収集と対応がますます重要となっている。
企業が成長し、社員が安心して働き続けるためにも、日本が、そして世界が何よりも平和であり続けて欲しい。海外進出によって生まれる海外メーカーとの新たな競合を乗り切り、さらに成長を続けるためには現在の技術力、品質、デリバリー等を改革していくことが必要になってくる。
未来へと引き継ぎたい100年の重み
100年の歴史の中で蓄積してきた技術力やノウハウを活かし、次の100年へと繋いでいくことこそ、私達に課せられた使命だと考える。
当社には鍛造品製造の長い歴史がある。特にハンマー鍛造には豊富な知識がある。人の手に頼らなければならない場面も多く、その技術には簡単にデータ化しにくい経験も必要とされる。技術者を育成するには時間もかかるため、即戦力を求める企業や大企業では簡単に参入しにくいニッチな分野でもある。このことは当社にとって大きな強味になっている。
さらに鍛造、熱処理、切削、加工段階での熱処理、研磨という一連の工程を一貫して製造できることも当社の強味となっている。一つの工程だけでは改善のできない場合であっても、前工程の工夫によって改善できることがある。また、作業の効率化、品質の向上のため、治具や工具の改良、製作を社内で行ってきた。これも大きな強味となっている。
一貫工程であるが故にできるこうした改善へトライする精神は100年という重みの中で醸成されたものである。この精神は今後も変えることなく未来へと引き継いでいかなければならない。引き継ぐことでこれまで不可能であったことや新しい分野の開拓に繋げられる可能性も出てくるだろう。
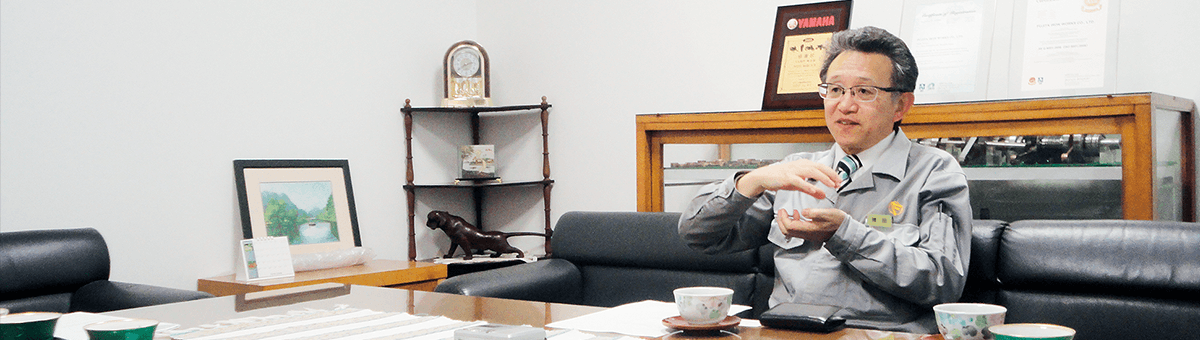
チャレンジし続けたい
これまでに多くのことにチャレンジしてきた。新しいことへのチャレンジは常に成功するとは限らない。成功の陰では多くの失敗も積み重ねられてきた。大切なことは失敗を単なる失敗に終わらせることなく、次の成功へと、いかにして繋いでいくのかだ。失敗があったからこそ、より素晴らしい技術を作り上げることができたとも言える。
取り引き先から新しい製品の製作が可能かどうかの問い合わせをしてくるのは、藤田鐵工所ならできるのではないかという期待感の表れでもある。こうしたときこそ、期待に応えられるようチャレンジできる絶好の機会となる。
国内でのものづくり環境はさまざまな要因で厳しくなっている。与えられた仕事をこなしているだけではチャンスは訪れない。チャレンジすればチェンジできる。そのためのチャンスはたくさんあるはずだ。将来への夢や可能性は、実は私達の足元にも転がっているのかもしれない。
時代の変化に柔軟に対応
企業として存続し発展していくため、今後も好むと好まざるにかかわらず、海外進出は必要になってくるだろう。それに伴い海外からの研修生などの受け入れも増加する。そうなった時、大切になってくるのが、コストや経営の効率化だけではなく、コミュニケーションだ。コミュニケーションを通してお互いの文化や歴史を理解することで信頼感も生まれてくる。
当社では社内のコミュニケーションも大切にして、営業と技術などの人事交流を進めてきた。こうした交流は組織の活性化に役立つだけではない。技術が分かっていれば取り引き先に対しても、新しい提案ができる。新しい提案が、新しい製品を生み出すことにもなる。これまで、全社的改善活動として4つのF作戦に取り組んできた。そして創立100 周年を機会にフレキシブル(柔軟に)を加えた。これからの時代は、柔軟な対応や発想などがますます重要となってくる。
藤田鐵工所はこの100年間、時代の変化に対し、自らも変化することで対応してきた。100年前、現在の藤田鐵工所の姿を想像できた人はいなかったはずだ。同じようにこれから100年先の藤田鐵工所の姿を想像することはできない。取り扱う商品は現在とは大きく変わっているかもしれない。場合によっては業態そのものも変わっているかもしれない。
100年先の藤田鐵工所が容易に想像できるような企業であってほしくはない。これからも激しく変化していく時代にあって、柔軟に対応していくならば、どのように変化していくのかは誰にも分からないからだ。ただひとつ言えることは、藤田鐵工所で働く全社員が、豊かで安心して平和に暮らすことができる企業であり続けたい、ということだ。